In the competitive world of cleaning tools, cleaning mop quality control is the cornerstone of manufacturing reliable, long-lasting products. From selecting high-quality mop fibers to refining designs based on consumer feedback in mop production, every step ensures that mops meet modern cleaning demands. Let’s dive into the meticulous process that guarantees excellence.
1. High-Quality Mop Fibers: The Foundation of Effective Cleaning
The journey begins with sourcing premium materials. High-quality mop fibers, such as microfiber blends or tightly spun cotton, are chosen for their absorbency, durability, and dirt-trapping efficiency. Advanced spinning techniques ensure uniformity in cotton yarns, while synthetic blends like polyester-polyamide create microfiber strands optimized for deep cleaning.
Manufacturers prioritize fibers that resist fraying and retain shape after repeated use, directly tying into cleaning control de calidad de fregonas protocols. Each batch undergoes stress tests to verify tensile strength and absorption rates, ensuring consistency before assembly.
2. Ergonomic Mop Design: Balancing Comfort and Functionality
An ergonomic mop design enhances user experience and reduces fatigue. Handles are crafted from lightweight yet sturdy materials like aluminum or reinforced plastics, with adjustable lengths to accommodate users of all heights. Prototypes are tested for grip comfort, weight distribution, and swivel mechanics to optimize maneuverability.
During production, attachment points between handles and frames are rigorously inspected. Methods like ultrasonic bonding secure mop heads to prevent detachment during heavy use—a critical aspect of cleaning mop quality control.
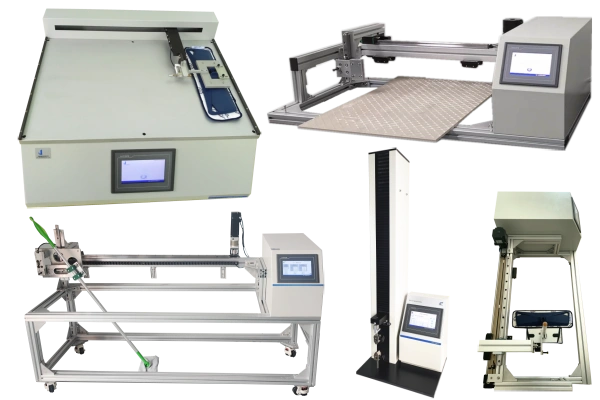
3. Precision Assembly and Quality Assurance
The assembly process focuses on durability and performance. Mop heads are evenly stitched or woven to ensure consistent fiber distribution, preventing uneven wear. Automated systems verify thread tension and bonding strength, while manual inspections check for defects like loose fibers or misaligned components.
Functional testing simulates real-world conditions:
- Swivel tests: Assess mop head flexibility.
- Weight tests: Confirm handle sturdiness.
- Absorption trials: Measure fiber efficiency.
Only tools passing these benchmarks advance to branding and packaging.
4. Consumer Feedback in Mop Production: Driving Innovation
Post-launch, consumer feedback in mop production becomes invaluable. Manufacturers monitor reviews to identify recurring issues, such as handle durability or fiber shedding. This data informs iterative improvements, such as reinforced stitching or eco-friendly material swaps.
For example, feedback on hard-to-replace mop heads has spurred designs with modular, snap-on attachments—enhancing sustainability and user convenience.
5. Sustainable Packaging and Global Distribution
Post-production, mops are packaged using recyclable materials to align with eco-conscious trends. Clear usage guidelines and care instructions extend product lifespan, reducing waste. A streamlined supply chain ensures timely global distribution while maintaining inventory accuracy.
Quality Control for Trusted Results
Cleaning mop quality control isn’t just a step—it’s a philosophy embedded in every phase, from fiber selection to post-purchase improvements. By prioritizing high-quality mop fibers, ergonomic designs, y consumer feedback in mop production, manufacturers deliver tools that simplify cleaning while standing the test of time.
Understanding this process empowers users to choose mops that combine innovation, durability, and practicality—transforming everyday chores into efficient, hassle-free tasks.